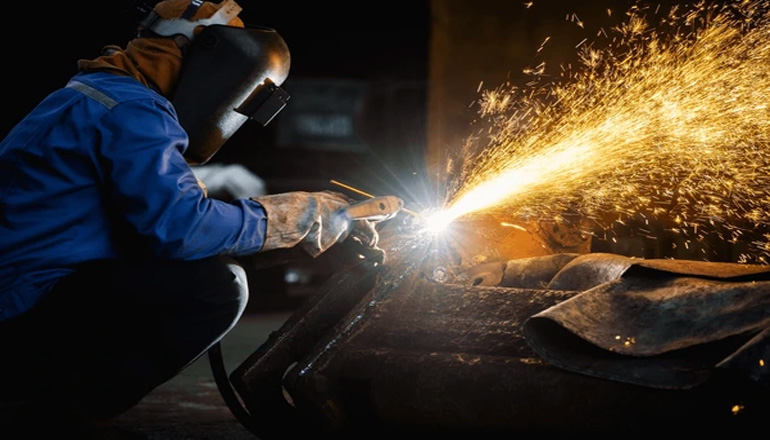
Carbon Steel Welding
Carbon steel is an alloy composed primarily of iron and carbon. It's the most common type of steel and typically contains low amounts of other alloying elements. It is one of the most widely used materials in construction, manufacturing, and numerous other industries due to its strength, durability, and versatility.
Keep in mind that all types of steel contain more than just iron and carbon. Modern steels only gain some of their strength from simple carbon additions but also from the added effect of small amounts of other alloying elements like manganese, silicon, chromium, molybdenum, vanadium, nickel, and copper.
Types Of Carbon Steel
As the amount of carbon in the steel increases, the steel becomes harder, which is desirable when a piece is exposed to high wear and tear. As a result, we're seeing three different types of steel:
- Low-carbon steel (less than 0.30% carbon)
- Medium carbon steel (0.30%-0.60% carbon)
- High carbon steel (0.60%-2% carbon)
Welding Mild Steel (Low Carbon Steel)
As noted, low-carbon steels contain up to 0.30% carbon, which makes them highly ductile and easy to weld. As a result, you don't need heat treatment before or after the welding, and you can weld mild steel with one of the four most popular methods, such as Gas metal arc welding (MIG), TIG, Stick, or Flux Core.
MIG welding mild steel is a common choice. It can choose matching filler metal according to the composition of the weld metal, and there is no pre or post-weld heat treatment required. Stick welding low-carbon steels is often preferred for quick on-field and outdoor repairs, and like with MIG, there are no specific precautions.
TIG welding is often preferred when welding exotic or non-ferrous metals since it offers excellent heat control and provides high-quality welds. Still, you can use it to weld mild steel or any similar welding project with thinner material.
Welding Medium/High Carbon Steel
Things get tricky once the carbon is over 0.30% in the steel. The carbon reduces ductility and increases the strength so that the welds can become highly brittle and susceptible to cracking. As a result, welding high-carbon steel can be challenging and requires specific welding procedures. To successfully weld steel with medium to high carbon equivalency, you will need the right filler metal, heat input, and heat treatment.
Filler Metal For High Carbon Steels
Medium/high carbon steels are exceptionally hard, and their tensile strength can reach 35900 – 484000 psi. When welding such a high-strength steel material, there are two ways of thinking in selecting the welding consumables. You can either choose a filler that matches the strength of the base metal or consider a cracking issue and choose a lower-strength filler metal.
However, of these two, it is more important to pay attention to the cracking risks of the welding joint. The harder the joint is, the bigger the chance that it will crack, so you will want to select the lower-strength filler metals when possible. As the joint has higher crack resistance, it is considered stronger, even if its overall strength is lower than two separate plates.
Additionally, when selecting filler for steel with higher carbon quantities, you should avoid using electrodes with excessive hydrogen content. Diffusable hydrogen can cause cold cracking, so low-hydrogen electrodes are typically the best choice.